3D Printing vs. Injection Molding
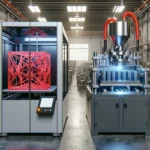
Manufacturing has come a long way from the days of assembly lines and manual labor. Today, the dynamic interplay between advanced manufacturing techniques like 3D printing and injection molding has reshaped the landscape, vastly increasing production speed and efficiency.
These manufacturing techniques take center stage while working on fundamentally different principles and catering to diverse needs. In this blog, we will delve into 3D printing vs injection molding, their similarities and differences, and the future for both manufacturing technologies.
3D Printing: Sculpting Possibilities Layer by Layer
3D printing is the process of creating three-dimensional objects from a digital file. Also known as additive manufacturing, it uses additive processes that involve laying down successive layers of material to create the desired 3D object. These layers can be seen closely as thinly sliced horizontal cross-sectors of the desired product.
There are many other variations of 3D printing technology, each suited to different applications and materials. Some machines work with metal, ceramics, sand, and biological tissue. Its applications continue to expand, with advancements in speed, materials, and printing techniques continuously being developed to improve its efficiency further.
Advantages
- Rapid Prototyping: 3D printing allows for the quick fabrication of prototypes, enabling faster iteration and testing of design concepts. This accelerates the development process and can shorten the time to market for new products.
- Complex Geometries: With 3D printing, one can create complex shapes and internal structures that would be impossible or prohibitively expensive to achieve with traditional manufacturing methods.
- Reduced Waste: Additive manufacturing adds material only where needed, often resulting in less waste than subtractive processes like CNC machining, which removes material from a solid block.
- Cost-Effective for Low Volumes: For small production runs or one-off items, 3D printing can be more cost-effective as it does not require the investment in specific tooling or setup costs associated with traditional manufacturing.
Disadvantages
- Scalability Constraints: While excellent for prototyping or low-volume production, it remains slower compared to conventional manufacturing techniques when it comes to high-volume production runs.
- Cost of Materials: Some 3D printer manufacturers mandate the purchase of proprietary materials, generally at a higher price than third-party alternatives. This makes 3D printing less cost-effective for mass production than traditional manufacturing’s economies of scale.
- Limitations in Print Sizes: 3D printing typically requires dividing larger objects into sections for assembly, potentially compromising structural integrity and aesthetics.
Use Cases
3D printing is a versatile technology that has a wide range of applications across various industries and fields. Here are some common use cases for 3D printing:
- Prototyping: One of the primary uses of 3D printing is rapid prototyping, which facilitates engineers and designers in swiftly creating models and prototypes for testing form, fit, and function. This accelerates the product development process, showcasing the efficiency of 3D print vs. injection molding in certain manufacturing phases.
- Manufacturing: 3D printing is used for direct digital manufacturing of final products, especially for complex or custom parts that would be costly or difficult to produce using traditional methods. It can also be used to create a 3D printed injection mold for injection molding.
- Healthcare: 3D printing has significant applications in healthcare, including the production of custom prosthetics, dental implants, and orthopedic implants. It’s also used for creating patient-specific anatomical models for surgical planning and education.
Injection Molding
Injection molding is a manufacturing process used to produce parts in large volumes. It involves injecting molten material into a mold, which cools and solidifies into the specific component’s shape.
The injection molding process is widely used for mass-producing components with unique or complex configurations. It is most commonly used with thermoplastics and thermosetting polymers but can also be used with metals, glass, and elastomers.
Advantages
- Mass Production Speed and Efficiency: Injection molding is ideal for high-volume production of parts with the same shape and dimensions. Once the mold is designed and created, millions of components can be produced with minimal variation between them.
- Complex Part Design: Injection molding can produce highly complex parts, incorporating intricate geometries that would be difficult or impossible to achieve with other manufacturing processes.
- Low Labor Costs: The injection molding process is highly automated. CNC machines can control the operation with minimal supervision, reducing labor costs compared to manual manufacturing processes.
- Tight Tolerances and Consistency: The parts produced have consistent quality and can be manufactured with tight tolerances, which is crucial for components that must fit together precisely in an assembly.
Disadvantages
- High Initial Costs: The need for new designs and high costs involved in 3D molding. Thus, short runs and prototype stages are not economically feasible for complex injection molding.
- Design Inflexibility: Once a mold is created, making design modifications can be costly and time-consuming due to the need to create a separate mold.
- Material Considerations: Not all 3D molding materials are created equal. Various properties and considerations have to be made before choosing a material, such as melt flow rate, thermal and chemical properties, and the desired characteristics for the finished product.
Use Cases
Key use cases for injection molding include the following:
- Automotive Industry: Injection molding is widely employed to manufacture a plethora of car components, including dashboards, bumpers, door handles, and various under-the-hood parts, showcasing its efficiency in contrast to traditional 3D print vs. mold methods for mass production in the automotive industry.
- Consumer Electronics: Many plastic parts in consumer electronics, like mobile phones, televisions, remote controls, and laptops, are made using injection molding.
- Aerospace: Precision parts for airplanes and spacecraft, often made from high-performance polymers, are produced using injection molding.
- Furniture: Many pieces of modern furniture incorporate plastic parts made using injection molding, such as knobs, handles, and structural components.
The Future of 3D Printing and Injection Molding
3D printing and injection molding are set to complement each other increasingly. 3D printing is evolving towards faster, larger-scale production capabilities, playing a vital role in rapid prototyping and complex, customized manufacturing scenarios. On the other hand, injection molding looks to remain the backbone of mass production as it is valued for its speed and efficiency.
The collaboration of these technologies will continue to be a highlight in areas like 3D printed injection molds for short-run injection molding, allowing for cost-effective experimentation and faster time-to-market. As materials and techniques advance, 3D printing will bridge traditional manufacturing, facilitating innovative design validation before committing to the economies of scale offered by injection molding.
Supercharge Your Manufacturing Capabilities With All-Plastics
All-Plastics is dedicated to propelling your production capabilities forward with scientific injection molding solutions. Our tailored injection molding services provide the versatility and precision required to elevate your manufacturing, regardless of industry. Reach your production goals by entrusting us with your project.
Please complete our online contact form to request a quote or more information about our services.