Injection Molding Troubleshooting Guide
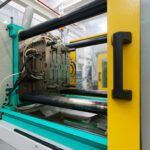
Injection molding is a highly efficient method of producing plastic components on a large scale, with consistent quality and low per-unit costs. It is widely used in various manufacturing sectors due to its precision engineering, repeatability, and scalability, which have transformed production lines worldwide.
Over the course of production, manufacturers often encounter various issues that can end up halting operations abruptly. These issues can lead to significant delays and increased costs, disrupting timelines and budgets. This is why it’s critical to resolve these technical hiccups swiftly and efficiently in order to maintain productivity and profitability.
In this blog, we’ve compiled a list of some of the most frequently encountered challenges in injection molding to help diagnose these issues quickly and prevent costly delays.
Why Regular Machine Maintenance is Important
Injection molding requires regular maintenance to ensure that the mold and machine function efficiently and produce high-quality parts. A well-maintained mold is crucial for consistent part quality and quicker cycle times, ultimately contributing to increased productivity. Machine maintenance is equally crucial since it addresses issues that can disrupt production and compromise efficiency.
By conducting routine checks and preventative measures, manufacturers can prevent problems that would otherwise require extensive troubleshooting, reducing downtime and production delays. Proactively caring for molds and machines ensures the integrity of the products and optimizes operational performance.
The long-term benefits of regular maintenance include enhanced reliability, reduced repair costs, and uninterrupted production schedules, all of which highlight its significance in sustaining the quality and efficiency of injection molding processes.
Optimize Your Manufacturing Efficiency With All-Plastics
All-Plastics provides advanced scientific molding solutions tailored to meet your production needs. Our cutting-edge micro injection molding technology enables us to deliver unparalleled precision and versatility to help you stay ahead of the competition. As industry leaders, we take quality control seriously, ensuring that every product meets our stringent standards.
Take your production efficiency to the next level with All-Plastics. Please fill out our online contact form to request a quote or more information about our services.
Common Issues in Injection Molding
Below, you’ll find some of the most common issues that lead to product defects during injection molding:
Problem | Cause | Solution |
Warpage – refers to the undesired deformation or distortion that can cause the parts to bend, fold, twist, or bow, leading to complications during the final assembly of the end product. | Under Packing | To better pack out the parts, increase pressures and times. |
High Melt Temperature
|
To minimize shrinkage, decrease melt temperature and increase cooling time.
|
|
Gate Freeze-Off
|
To increase the amount of time there is to fill and pack, consider increasing gate size or decreasing land length.
|
|
Unbalanced Runner | Ensure that all cavities fill at the same rate by adjusting the volumes of the runner system. | |
Non-Uniform Cooling | Check the line layout and measure the temperature and water throughput of each half. | |
Over Packing | To reduce molded-in stress, back off the second-stage time and pressure. | |
Insufficient Feed | Increase shot size and/or decrease cushion to push more resin into the cavity. Ensure consistent cushion size. | |
Insufficient Pressure | Increase the screw forward time under pressures to ensure gate freeze-off is obtained. | |
Cold Mold | Slow the cooling/increase mold temp so that the outer skin and the interior of the part shrink at the same rate. | |
High Melt Temperature | Lower the melt temperature to, in effect, lower the amount of heat that needs to be pulled from the part. This will help reduce differential cooling and shrinkage. | |
Runner & Gate Size | Increase the runner and gate sizes to get best pressure transfer to the part in the cavity of the mold. | |
Poor Part Design | Use nominal wall design principles with standing features at 50% of nominal wall thickness. | |
Bubbles and Voids – trapped air or insufficient material creates hollow areas within a molded part. Bubbles typically surface as spherical cavities, whereas voids are larger, irregularly shaped cavities found within the core.
|
Low Pressure | Can be resolved by increasing injection, hold and pack pressures and times. Part weight should also be monitored until it plateaus to ensure complete cavity filling through gate freeze-off. |
Insufficient Volume | Can be addressed by increasing shot size and/or lowering the cushion to allow more rein volume into the cavity. | |
Low Mold Temperature | Increase mold temperature to slow down the cooling of the skin, making the material inside less prone to pulling away from itself. | |
High Melt Temperature | Decrease melt temperature to ensure minimal shrinkage and faster curing of the part. | |
Thick Wall Sections | Design the part with uniform wall thickness, ensuring ribs are on 50% of nominal wall thickness. | |
Burn Marks – characterized by black or rust-colored discolorations on the final plastic product.
|
High Injection Velocity | Lower the injection speed to allow trapped air in the mold to escape and reduce the shear heating of the resin. |
Insufficient Venting | Increasing the size, number and/or changing the location of the vents. | |
Excessive Residence Time | Reduce the amount of time the resin stays in the barrel by speeding up the cycle or decreasing the barrel size. | |
Excessive Melt Temperature | Lower the barrel heaters, screw speed, and the back pressure to reduce resin temperature. | |
Damaged Heater Band | Damaged heater bands can be checked and replaced if necessary to prevent overriding or burnout. | |
Dead Zones | Inspect the resin’s path to ensure there are no dead zones present to prevent collecting and degrading material that breaks free on injection. | |
Color Inconsistencies – pigment distribution in molten plastic is uneven, leading to variations in hue or intensity across different parts of a molded item.
|
Contamination | Purge out the injection barrel until the resin runs clean. |
Burning | Lower the melt temperature, screw speed, and/or back pressure. Injection velocity can also be decreased. | |
Long Residence Time | Reduce the cycle time. Use a small-volume barrel. You can also use a reverse temperature profile. | |
Not Enough Heat Soak | Movieto a larger barrel volume to aid the dispersion of additives and reduce severe shear heating when the shot capacity is too small. | |
Heater Band Override | Verify the proper screw design and raise the rear zone temperatures to lower the viscosity of the resin and shear effects. |